The 120-mile-long New Madrid Seismic fault line is one of the most prominent and historic seismic zones east of the Rocky Mountains. The probability of soil liquefaction and consequent above-ground structural damage and/or settlement during a seismic event often requires ground improvement for buildings supported on shallow foundations.
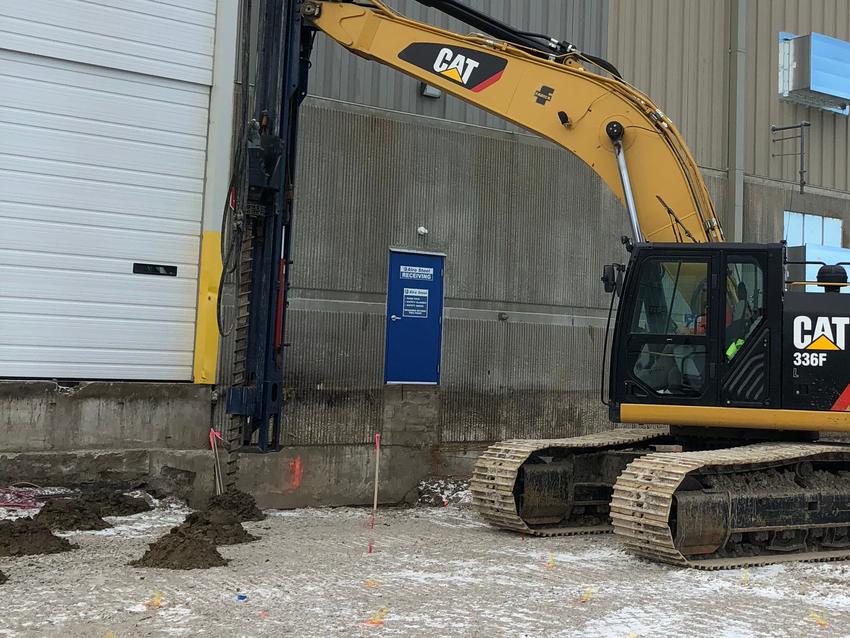
The project
Construction of a 66,000-sq. ft steel-frame warehouse on shallow footings was planned at an existing steel fabrication facility in Earth City, MO, which lies within the New Madrid seismic zone. The warehouse was to be constructed over a subsurface profile consisting of 12 ft of loose/soft silt and lean clay over 13 ft of potentially liquefiable loose to medium dense saturated sand. Beneath the liquefiable saturated sand, medium dense to dense sand extended to the bottom of the borings. The presence of the potentially liquefiable layer meant that ground improvement was required to mitigate the effects of liquefaction during an earthquake event.
The challenge
- The warehouse was an addition to an existing building. Minimizing vibration and settlement risk to the in-place structure during ground improvement was critical.
- The work also had to be staged to accommodate the logistics of the operational facility.
The solution
The General Contractor for the project, who was familiar with Keller’s range of ground improvement options, requested input into developing the best approach for this project. After considering several alternatives, Keller provided a design-build earthquake drain option that would mitigate liquefaction by limiting excess pore pressures generated during a seismic event to levels less than the liquefaction threshold. Over 2000 earthquake drains were installed on a 6-ft triangular pattern to a depth of about 30 ft across the building footprint. To alleviate concerns about the use of vibratory installation methods close to the existing building, Keller predrilled all locations within 15 ft of the structure, taking care to avoid disturbing the saturated soils. Close collaboration with the owner and general contractor allowed the work to be sequenced to accommodate the facility’s operational logistics.
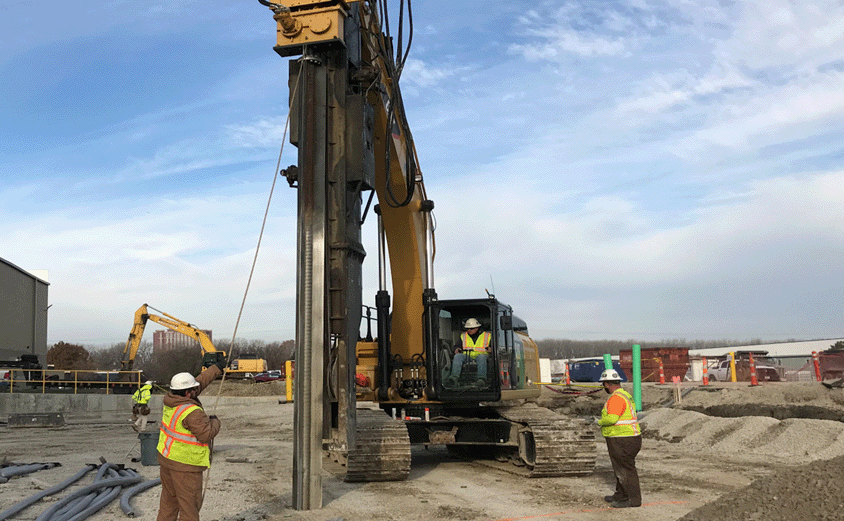