Permeation grouting (cement grouting, chemical grouting, or pressure grouting) fills cracks or voids in soil and rock, permeating granular soils with flowable grouts to create a cemented mass.
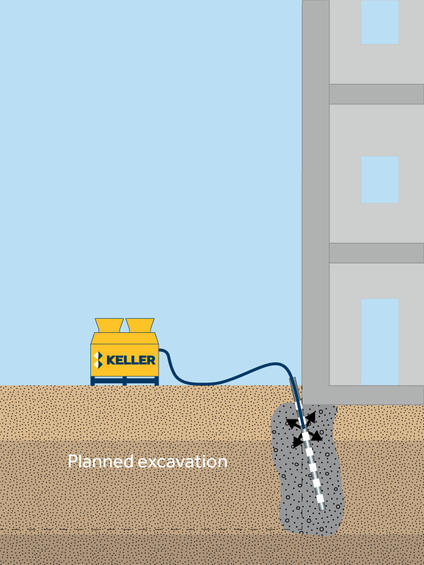
Common uses
Process
Chemical grouting transforms granular soils into sandstone-like masses by filling the voids with low viscosity, non-particulate grout. Sands with low fines content are best suited for this technique. Typically, a sleeve port pipe is first grouted into a pre-drilled hole. The chemical grout is injected under pressure through the ports. The grout permeates the soil and hardens, creating a sandstone-like mass. The grouted soil has increased strength, stiffness, and reduced permeability.
Chemical grouting offers the advantages of being easily performed where access and space are limited and no structural connection to the foundation being underpinned is required. A typical application of chemical grouting is to provide excavation support and underpin existing structures adjacent to an excavation. It can typically be accomplished without disrupting normal facility operations.
Chemical grouting equipment is suited for tunneling applications in urban environments, whether for stabilizing soil around break-ins or break-outs or mitigating settlement of overlying structures within the influence of the tunnel alignment.
Specialist contacts
Lucian Spiteri | Chief Grouting Engineer | 973-417-1667
Max Pucciarello | Senior Design Engineer | 973-897-4101
Advantages
Quality assurance
Keller has developed proprietary equipment and software (iGroutTM) to allow real-time monitoring of all parameters during the chemical grouting process. The operator can adjust the parameters (such as mix type, flow rate, pressure, and volume limits) based on the real-time acquisition of drilling and grouting data while simultaneously monitoring for any movements or deflections of the ground or nearby structures. Data collected during drilling and grouting is recorded on a server that produces grouting reports and CAD drawings. This advanced monitoring and control system increases chemical grouting accuracy, efficiency, and quality control while reducing risk.