High mobility (cement slurry) grouting, or cement or rock grouting, is usually done in fissured rock to reduce water flow along the joints and discontinuities in the rock. Occasionally, cement grouts are injected into the void space within coarse granular soils.
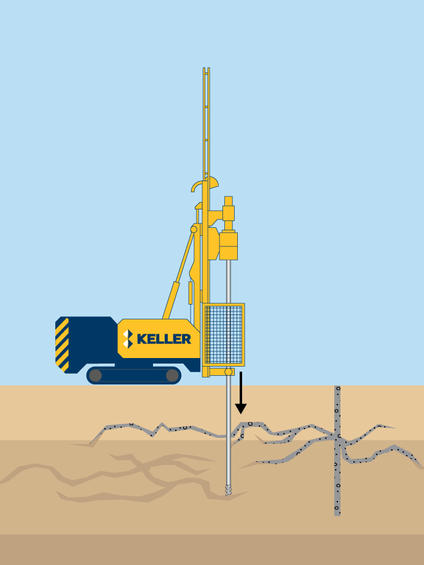
Common uses
Process
High mobility grouting fills pores in granular soil or voids in rock/soil with flowable particulate grouts. The grout particle and void sizes must be appropriately matched to allow the cement grout to permeate. Depending on the conditions, Portland cement or microfine cement grout is injected under pressure at strategic locations through a single port or multiple port pipes. The grouted mass has increased strength, stiffness, and reduced permeability.
Cement grouting can offer an economic advantage for underpinning applications over alternative approaches such as removal and replacement or piling. It can be performed where access is complex and space is limited. Since the effectiveness of cement grouting is independent of structural connections, this technique is readily adaptable to existing foundations and can typically be accomplished without disrupting normal facility operations.
Specialist contacts
Lucian Spiteri | Chief Grouting Engineer | 973-417-1667
Max Pucciarello | Senior Design Engineer | 973-897-4101
Advantages
Quality assurance
Keller has developed proprietary equipment and software (iGroutTM) to allow real-time monitoring of all parameters during the cement grouting process. The operator can adjust the parameters (such as mix type, flow rate, pressure, and volume limits) based on the real-time acquisition of drilling and grouting data while simultaneously monitoring for any movements or deflections of the ground or nearby structures. Data collected during drilling and grouting is recorded on a server that produces grouting reports and CAD drawings depicting a visual representation of the completed work. This advanced monitoring and control system increases the accuracy, efficiency, and quality control of cement grouting.