Installation of a 600-foot long, permanent biopolymer collection trench and barrier curtain wall for environmental remediation at the Bayway Refinery.
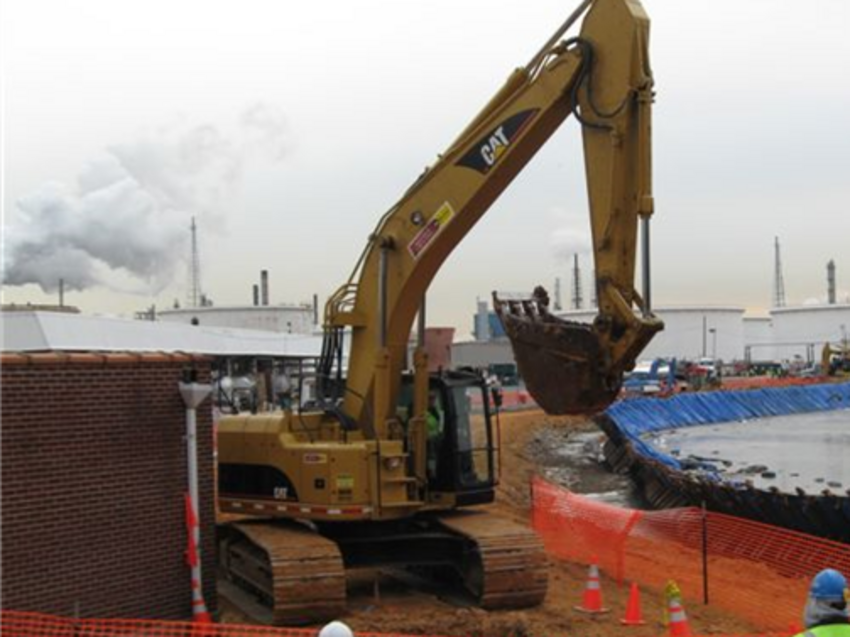
The project
EPA-directed environmental remediation at the Bayway Refinery by former owner ExxonMobil included collection and removal of impacted groundwater at the refinery’s Domestic Trade Terminal. To achieve this, the engineering and construction firm of Camp Dresser and McKee (CDM) specified the installation of a 600-foot long, permanent biopolymer collection trench and barrier curtain wall.
The challenge
The challenge was to construct a feature along 600 ft of site perimeter which could both collect contaminated groundwater and provide a barrier to prevent both off-site migration of contaminated ground as well as collection of clean groundwater from outside of the limits of contamination.
The solution
Biopolymer collection trenches are installed using the same basic construction methods as soil-bentonite slurry trenches. During excavation, trench wall stability is maintained by a viscous slurry. As excavation progresses to full depth, backfill material is introduced which displaces the slurry. For collection trench construction, the use of biodegradable slurry to stabilize the trench walls, together with suitable permanent drainage material for the backfill, allows groundwater to flow freely into the trench and into the collection system. An impermeable liner installed on the down gradient trench wall prevents any groundwater migration beyond the trench.
Prior to any trenching, Keller installed a temporary dam system along the trench alignment to retain the water in an adjacent pond and protect the work area from flooding. Keller then installed a stable working platform, 25 feet wide and up to 7 feet deep, between the temporary dam and the trench alignment. Slurry trenches, by design, are typically keyed into an impermeable stratum to ensure a complete cut-off. The EPA permit required that the bottom three feet of the trench, which included the 2-foot deep key, should be concrete in order to seal the trench liner into the underlying dense till. As a more cost effective alternate, Keller proposed to place a 3-foot layer of 1.5-inch diameter stone to the required depth during backfilling operations and post-grout the stone once backfilling for the entire trench was complete. Pre-excavation work included field bench testing of the grouting method to determine the pore volume of the stone so that the theoretical volume of grout needed to create a watertight seal could be calculated.
Restricted access created by the pond on one side of the work zone and refinery fueling stalls on the other, a layer of unanticipated miscellaneous construction fill in the top eight feet of portions of the trench alignment, and working in winter weather conditions added to the challenge of the project.
Excavation was accomplished under guar slurry delivered to the trench from a 10,000-gallon holding and pre-mixing tank. Impacted spoils were trucked off site for disposal. As the trench was advanced, 18-foot wide, 80-mil HDPE interlocking liner panels were installed using a pre-fabricated frame system. The stone base was then installed, ensuring that the liner stayed in place once the frame was removed. As the liner was placed, vertical perforated piping with a 2-foot horizontal stick-up was installed on 5-foot intervals for the subsequent grouting program.
Prior to drainage material placement, temporary slotted well screens were installed through which a water/enzyme mixture would be circulated once the trench was complete to accelerate the guar breakdown. Drainage backfill was then placed to the invert elevation of the collection pipe. The pipe was then placed in the trench and backfilling continued up to the finished elevation. As excavation progressed along the alignment, samples were taken from the underlying dense till to ensure the trench was keyed into the proper material. Viscosity, pH and specific weight of the biopolymer slurry were tested on an on-going basis and as-built measurements were taken during the installation of the trench and collection pipe. During grouting, grout samples were retrieved daily and laboratory tested to verify the required strength had been achieved. When grouting was completed, measurements were taken from installed tell-tale pipes and plotted graphically. These measurements, together with the comparison of actual theoretical grout takes, determined if additional grouting was required.
The collection pipe was connected to a 48-inch diameter HDPE manhole, installed at one end of the trench, from where impacted groundwater was pumped to the on-site treatment plant. Free phase petroleum product was collected in the installed 8-inch sumps and pumped off for treatment.