The C$13 billion Eglinton Crosstown is a new 19km light-rail line that extends Toronto’s public transport system west, adding 25 stations and creating commuter links with the city’s subway and bus routes.
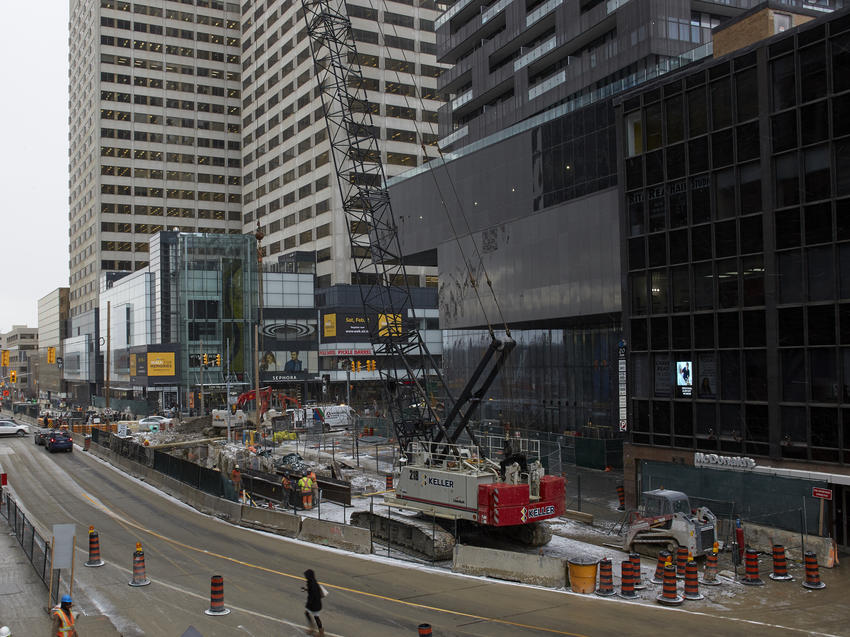
The project
Part of the project includes the construction of an underground tunnel and a new station (Yonge Station) in downtown Toronto below an existing subsurface station at Eglinton Ave. Construction and excavation for Yonge Station extended approximately 853 ft (260m) along Eglinton Ave. with a maximum subway platform depth of 72 ft (22m) below the existing street grade.
The challenge
The new LRT line intersected beneath the existing Toronto Transit Commission (TTC) subway tunnel at the Yonge and Eglinton intersection. The support of the excavation (SOE) system had to be designed to resist hydrostatic pressure and earth loading, groundwater cut-off, and supporting loading from traffic decking, construction equipment, soil stockpiles, existing structures, and existing utilities and services. Additionally, the existing station required underpinning support during excavation beneath it.
The solution
Keller provided design-build watertight support of excavation (SOE) for the construction of the proposed Yonge station and the underpinning of the existing station, including a 30m-deep secant pile shoring system to facilitate the excavation. As excavation progressed, Keller added internal bracing, soldier piles and lagging, and jet grouting to close gaps around existing utilities. Traffic decking and king piles were used to support traffic and existing utilities safely.
To support the tunnel and main entrance structure, slurry-drilled caissons (drilled shafts) were installed. For tunnel excavation below the existing subway tunnel, Keller installed shotcrete, a micropile cut-off wall, additional soldier piles and lagging bracing and struts, and soil anchors.
Working in a congested area of downtown Toronto, the team had limited space for equipment and had deliveries made at night. A heightened safety awareness was taken with pedestrians and traffic close to the site.
Instrumentation installed on existing structures to monitor any movement in real-time. An extensive Quality assurance and quality control program was implemented during all construction activities. The alignment of the secant piles and jet grout columns was measured and used to generate an as-built 3D profile. Supplemental jet grout elements were installed based on the detailed 3D profiling.
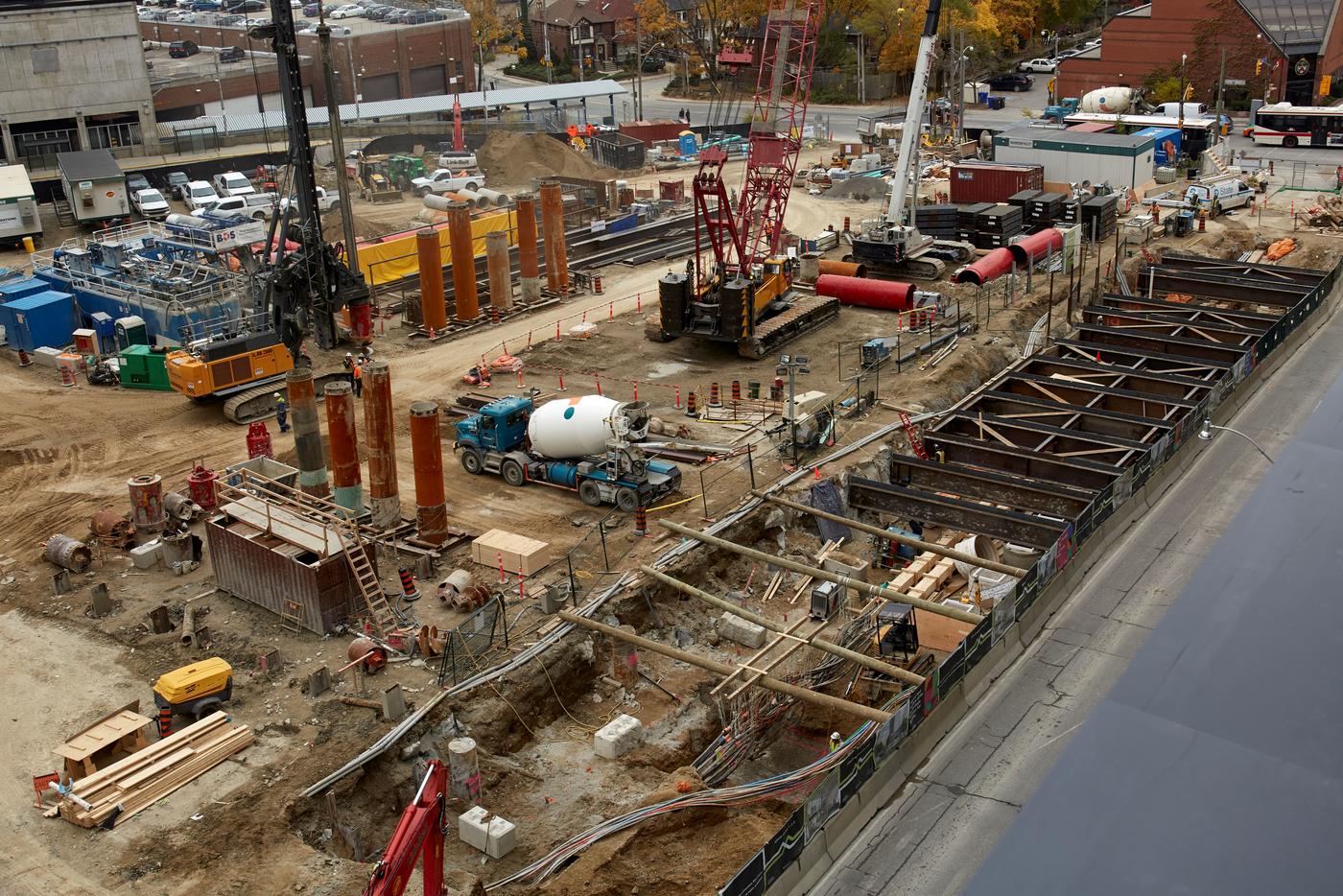