Keller developed a liquid nitrogen ground freezing solution that allowed for safe access to inspect and repair the tunnel boring machine (TBM) cutter head that experienced mechanical failure during mining operations.
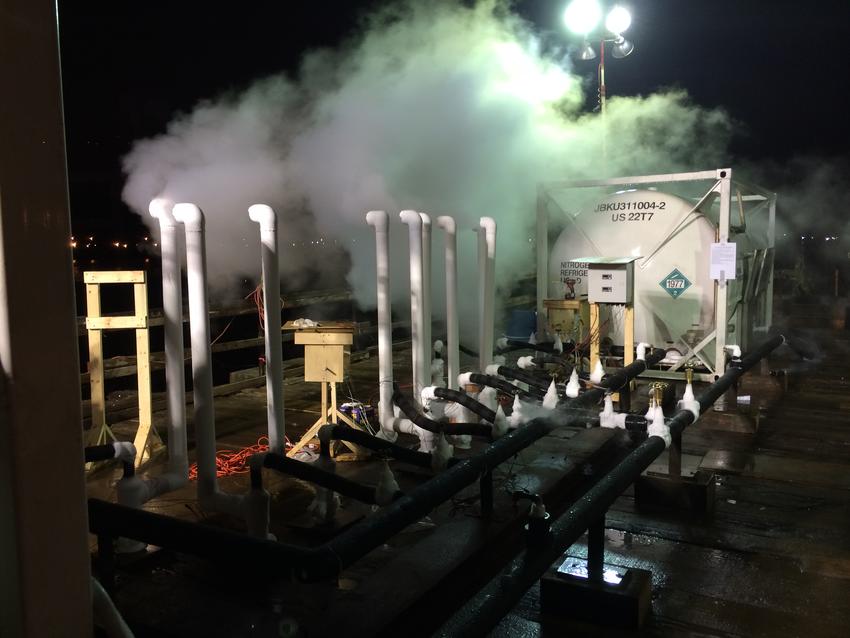
The project
The Port Mann Water Main is designed to more than double the capacity of the existing system to accommodate future growth. The 7 ft (2.1 m) diameter steel water main itself lies within an 11.5 ft (3.5 m) diameter, 3,280 ft (1.0 km) long tunnel mined between deep vertical shafts constructed on the north and south banks of the Fraser River.
The challenge
Mining was well underway, and the Earth Pressure Balance tunnel boring machine (EPBM) was approximately 160 ft (48 m) below the river mud line and 650 ft (200 m) from the north bank exit shaft when an unanticipated mechanical failure occurred in the cutterhead halting mining operations. Initial approaches to access the EPBM included dewatering the soil formation to provide a watertight zone around the cutterhead and depressurizing the cutterhead itself. However, these options were ultimately ruled out due to environmental issues.
The solution
The general contractor contacted Keller, who developed a liquid nitrogen ground freezing solution that allowed safe access for inspection and repair and quick implementation by isolating the cutterhead from the surrounding earth and hydrostatic pressures.
This project was the first time a freeze had been attempted in the middle of a river. The ground freezing work had to be accomplished from a pile-supported platform installed through the water directly above the stalled EPBM, presenting several following logistical challenges:
- All equipment and materials, including the drill and liquid nitrogen storage tanks, had to be crane-lifted onto a barge, transported to the working platform, and off-loaded by service crane.
- Lack of consistent local supply and transportation cost considerations meant liquid nitrogen had to be trucked from Seattle, WA. The liquid nitrogen supply needed to be refilled day and night during freeze build-up and daily during the maintenance freeze period, requiring frequent barging of supply tankers to the work zone.
Because of the extremely low temperatures that can be achieved, liquid nitrogen was used as the cooling agent to close the freeze in days rather than weeks, which would be needed with brine.
The ground freezing program was focused on creating a block of frozen soil to encapsulate the cutterhead, providing a watertight cut-off and alleviating the hydrostatic pressure. Keller’s design consisted of 11 freeze pipes installed 10 ft (3 m) below the EPBM invert and spaced 3 ft (1 m) apart in plan. Monitoring pipes instrumented with resistance temperature devices (RTDs) were incorporated into the design to measure ground temperatures. Thermal finite element modeling (FEM) was used to determine the time and cooling effort required for freeze formation. The final design consisted of a discrete block of frozen soil 29.5 ft (9 m) in height, 23 ft (7 m) in width, and 6.5 ft (2 m) thick.
Drilling and freeze pipe installation was round-the-clock, with several quality control measures instituted to ensure a smooth operation. An 8-in. (200 mm) diameter surface casing was installed through the working platform and set to 5 ft (1.5 m) below the mud line and surveyed with inclinometers. The 6-in. (150 mm) sonic drill outer casing and 4-in. (100 mm) core barrel was advanced incrementally to design depths as the soil was extracted. Surveys were made at the mid-point and immediately above the TBM to verify clearance and ensure that the pipes were close enough to the TBM face to achieve a proper freeze closure to the cutterhead. The freeze pipes were instrumented with thermocouples placed every few feet to verify that the liquid nitrogen was maintained at a level sufficient to fulfill the design objective yet not extend the freeze outside the target zone and control nitrogen flow to individual pipes.
The liquid nitrogen was delivered to drop pipes within the individual freeze pipes via an on-deck distribution manifold. Gas generated as the liquid nitrogen boiled traveled up the annulus between the freeze and drop pipes and was vented to the atmosphere. After 12 days of freezing, the temperature data indicated that the freeze was sufficiently formed to allow safe entry into the cutterhead chamber to begin repair work. The freeze was discontinued after the repairs, and tunneling operations could resume immediately.
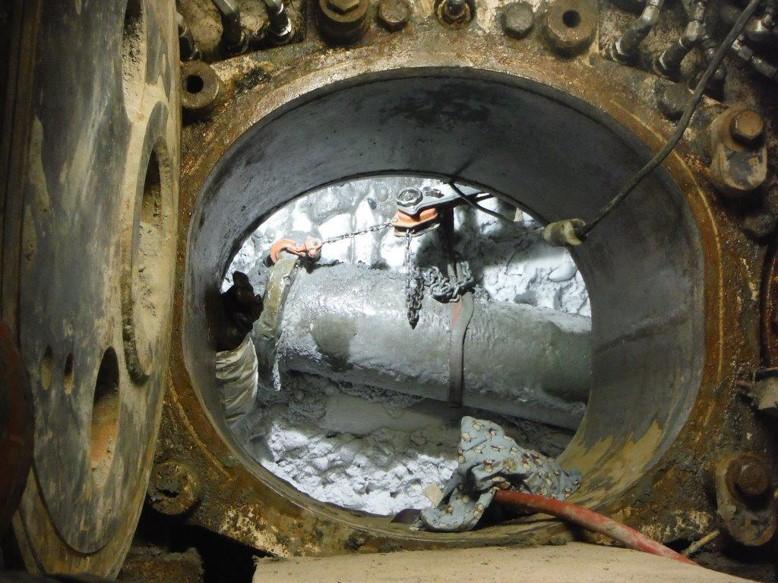