Keller’s deep well depressurization system, installed ahead of schedule, prevented the heaving of challenging lower Potomac soils while constructing a new CSO facility that will reduce pollution of the Potomac River and streams.
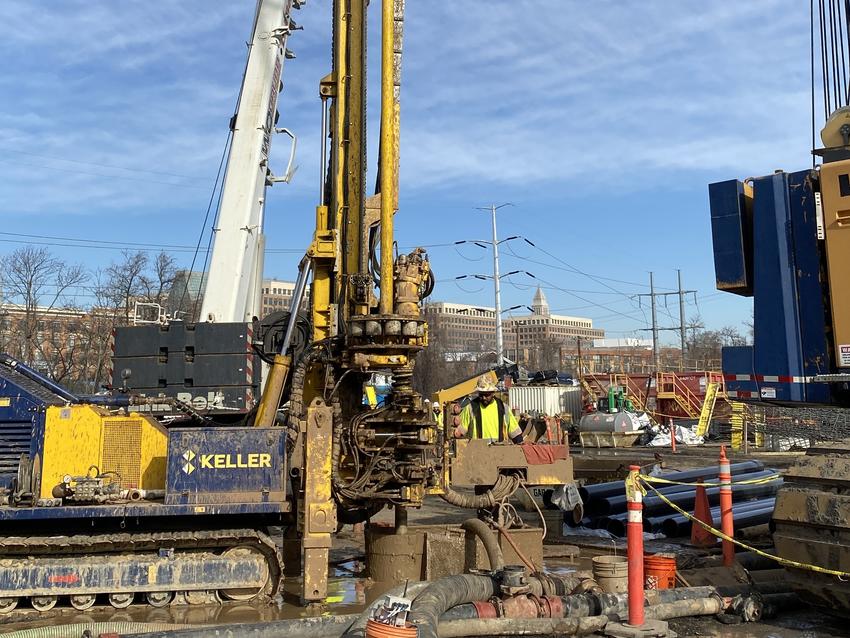
The project
To manage combined sewage overflows into the Potomac River and other nearby waterways, the City of Alexandria initiated RiverRenew, the largest infrastructure project in its history. Part of the project was constructing a pump station within two shafts (one 72-ft and one 40-ft diameter) to approximately 160 ft below grade. The shaft excavations would be supported by circular diaphragm walls extending to approximately 175 ft below grade.
The site geology generally consisted of fill, marsh deposits, alluvium, terrace deposits, upper Potomac soils (largely high plasticity clays), and lower Potomac soils (largely clayey sand and silty sand). The upper Potomac soils are impermeable relative to the underlying lower Potomac soils. The static groundwater level measured in the lower Potomac soils was approximately 27-ft below grade.
The challenge
Meeting design parameters and other constraints based on subsurface and site conditions would require the right combination of geotechnical construction techniques for groundwater control, ground improvement, support of excavation (SOE), and deep foundation elements. For instance, the lower Potomac soils required depressurization at the pumping and screen shaft locations (part of the new pump station facility) to prevent heaving during shaft excavation.
The solution
Keller provided several scopes on this project, including constructing diaphragm walls for the shafts, installing deep wells for depressurizing the Lower Potomac soils during shaft excavation and lining activities, and treating the dewatering effluent before discharging it to Hoffs Run, a local tributary.
To prevent basal instability during the excavation of the pumping and screen shafts, Keller depressurized the lower Potomac soils (from 187 ft to 300 ft below grade) by installing a pressure relief dewatering system comprised of one existing pump test well and nine 260-ft, 8-in. diameter deep wells, approximately 40 ft on center to center spacing along the combined perimeter of the pumping shaft and screening shaft, and outside of the slurry walls. The wells were installed by mud rotary drilling within a 16-in. diameter borehole using a guar gum-based polymer drill fluid. Each well was equipped with a submersible turbine pump and discharge piping plumbed to a common PVC discharge manifold routed to the approved discharge location.
When the deep well drilling operation mobilized to the site, the diaphragm wall work was ongoing, and the workspace was extremely limited. Therefore, choreographed site coordination was critical with constant communication between site team leaders needed to keep the operations safe and productive. Some drilling standby occurred when the 170 ft diaphragm wall rebar cages were picked and lowered into the slurry trenches and during hydromill equipment relocation.
During well screen and casing installation, Keller had to find the proper mud weight and viscosity balance to maintain borehole integrity. Some minor borehole sidewall sloughing was experienced, which required redrilling. Despite these challenges, Keller completed the drilling of the wells ten workdays ahead of schedule.
The system fully met the project team’s expectations. The initial system flow rate was 1,350 GPM, which dropped to a steady state flow rate of 700 GPM. Groundwater levels in the lower Potomac soils dropped from 27 ft below grade to 130 ft below grade in the first week of pumping, then gradually dropped to 160 ft below grade over the next two months.
To effectively process and treat groundwater generated from tunneling activities, Keller also designed, fabricated, and supplied four temporary water treatment systems. The systems were designed to remove free non-emulsified oil and grease, total suspended solids (TSS), and pH adjustment. The four treatment plants were located strategically throughout the project to allow multiple aspects to be completed simultaneously. They were built within insulated, temperature-controlled cargo containers for year-round use and easy relocation of the systems if required.