Keller's consistency and focus, careful attention to safety protocols, equipment staging, and operational procedures throughout a four-year scope of work mitigated impact to the surrounding communities.
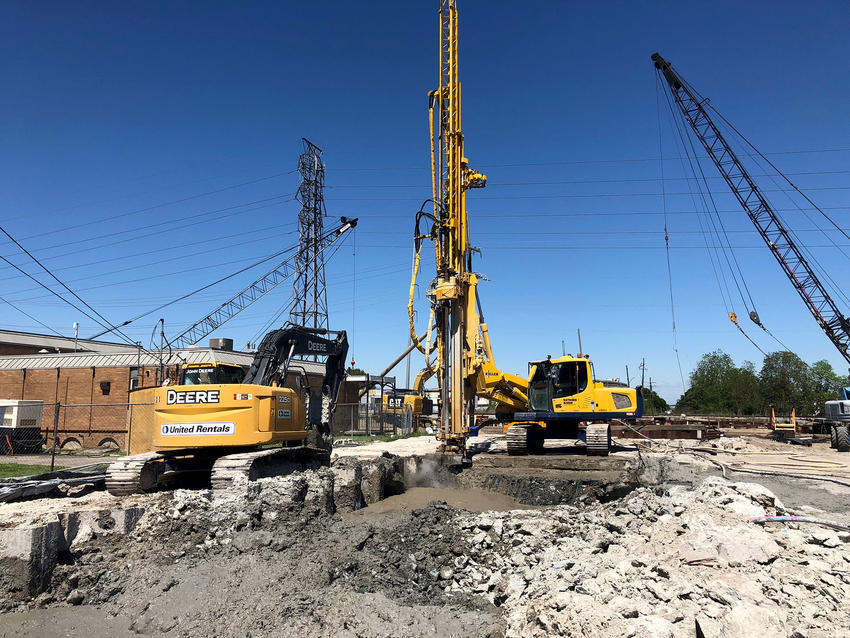
The project
The ongoing Southeast Louisiana (SELA) series of flood control measures are designed to upgrade the City of New Orleans’ extensive network of underground box culverts and pumping stations. The improvements, which are designed to minimize flooding during heavy rain events, are administered under a project cooperation agreement between the Sewerage and Water Board of New Orleans and the US Army Corps of Engineers (USACE), which is the agency responsible for design and construction of flood protection in the greater New Orleans area.
The challenge
The City of New Orleans lies below sea level. The water table is located just below the ground surface. Therefore, groundwater control to ensure a dry excavation was a critical aspect of the construction program. The trench alignments ran through heavily trafficked residential and commercial uptown areas. Traffic flow required constant maintenance along the city streets and major intersecting streets. This requirement added to the challenge from the constructability and operational perspective. Protection of vehicular and pedestrian traffic in the active construction zones was also a high priority.
The solution
As part of the overall program, many of the streets required sheeted excavations for the construction of underground box culverts. To reduce water infiltration into the excavations for the cast-in-place culverts, the USACE specified jet grouting to construct bottom barriers for lateral support and seepage mitigation. In addition to groundwater control, the bottom barriers provided structural support for the in-place culvert sections. Keller was awarded the contracts for jet grouting work along Napoleon and Louisiana Avenues and Desire and Montegut Streets. At times, multiple full crews were required when work in different areas was concurrent.
Extensive planning and preparation were required to ensure that all of the owner’s public safety and traffic flow concerns were addressed and disturbance to local residents and businesses was minimized. Measures included the implementation of dust and noise control. Efficient equipment set-up and management within the limits of the median work areas were also required for Keller to pump grout up to 1,000 ft from the batch plant. This reduced the number of plant moves necessary over the duration of the jet grouting work.
Prior to production jet grouting, test sections were constructed to verify that the operational parameters selected (flow, pressure, etc.) would successfully construct the required column diameters. During production work, overlapping 13 ft and 15-ft-diameter Superjet columns were installed within the sheet piling, with column diameters and plan configurations tailored to the specific box culvert/trench size. Quality control measures included wet grab sample retrieval and testing and frequent specific gravity checks. Core samples were taken at the rate of one per 20 installed columns and tested for unconfined compressive strength and permeability.