As the high-profile Miami skyscraper celebrates its official opening, we look at back at how Keller provided a range of techniques and overcame numerous challenges to help create a modern masterpiece.
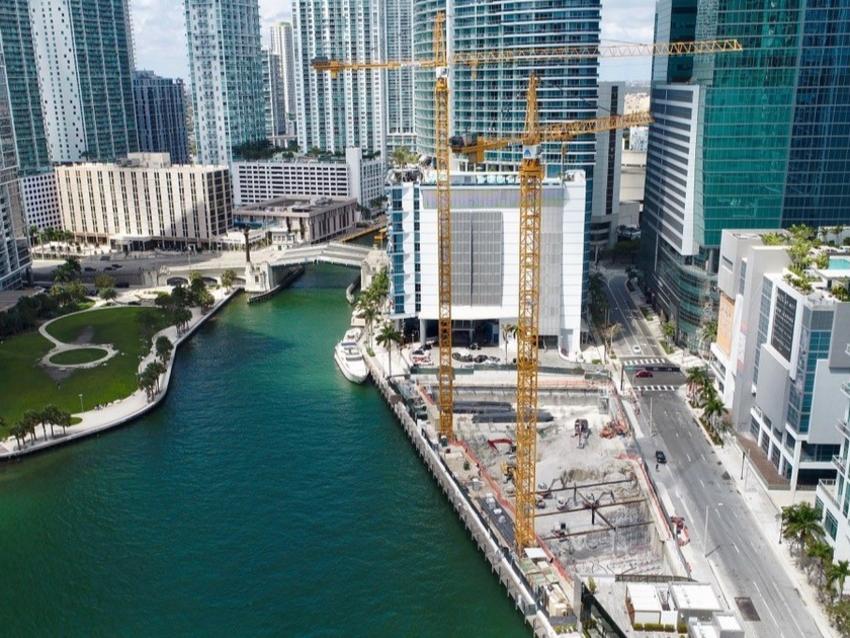
It’s the epitome of luxury living and America’s tallest all-residential building south of New York. A gleaming 66-story, sail-shaped tower overlooking Miami’s Biscayne Bay.
The Aston Martin Residences is the iconic British carmaker’s first foray into the real estate market and features 391 units, including seven penthouses with private pools. The largest of these apartments will set you back tens of millions of dollars – and comes with an Aston Martin racing car, of course.
The property officially opened in late April to coincide with Miami hosting the Formula One Grand Prix and has taken around six years to build. While it’s the opulent architecture and lavish design details that have grabbed the headlines, beneath the surface is an equally impressive geotechnical solution that helped take this building from concept to reality.
A giant ‘bathtub’
Despite the tower’s imposing presence, it actually sits on a compact 131 ft by 279 ft wedge-shaped site in one of the busiest parts of Miami. With the water level just 1.6 ft below the surface and the building requiring a 6m excavation, Keller proposed an innovative ‘bottom seal’ solution – like a giant bathtub – to control water flow.
This technique involved underpinning the existing buildings on either side of the site with permeation grouting and then installing more than a thousand deep soil mix (DSM) columns. Multiple GPS units were used to ensure the correct layout, while one percent of the columns were cored to confirm the compressive strength met design parameters.
However, this phase wasn’t completely straightforward, as Senior Project Manager Nick Feldt explains: “During pre-drilling for the DSM columns we encountered a number of obstructions, such as old piles and rebar. So to fill in the gaps the DSM tool couldn’t penetrate, we used down-the-hole hammers to pre-drill most of the obstructions and to jet grouting – 70 columns, 3.94 ft in diameter – which encapsulated the existing obstructions and sealed the ground.”
In addition, the client – main contractor Coastal Construction – required shallow ‘bottom plug’ holes (7.6m by 7.6m) to allow foundations for the two massive construction cranes. Keller created a tremie seal – a concrete slab placed underwater. Once the concrete reached the required strength, the water was pumped out leaving dry holes for the foundations.
A novel solution
To create the retaining wall for the basement’s excavation, the team mainly used a twin axis soil mixing method, installing 171 columns around the site perimeter reinforced with wide-flange beams.
“On the south-west portion of the site, where another tower sits adjacent, there wasn’t enough space for this technique,” adds Nick. “So we installed 75 cased continuous flight auger (CFA) piles instead. We then moved on to the piles for the main tower foundations. However, because of the site’s small size and the proposed building’s high loads, we simply didn’t have enough space to install typical CFA.
“Working with the client, our Miami Keller experts proposed what, at the time, was a relatively new technique that we’d developed internally – tangent bearing elements (TBEs). This method allows you to closely group together cast-in-place elements, drilled with an auger, to support the loads in a confined area. In total, we constructed more than 500 of these.”
Finally, the team excavated the entire mat foundation before turning it over to Coastal for one of the largest concrete pours the city had ever seen.
“This was a mammoth project for Keller, lasting over 19 months and involving multiple techniques, as well as logistical and locational challenges,” he says. “We partnered with the client at every stage to overcome hurdles and offer solutions that ensured the project kept on track.
“Today, we’re delighted to see the finished building open and we’re proud that Keller innovation and hard work has played a major part in its development.”